For the widespread use of electronic systems to take off in the aviation industry, safety must first be extensively proven. The nature of air travel means that operators must be certain that devices won't fail. To ensure this, comprehensive testing must first take place in labs and manufacturing facilities.
Our programmable power instruments allow virtually any AC or DC waveform to be created. Component performance can be analysed under difficult scenarios such as brownouts, to see if it is fit to fly. Besides test equipment, we also provide a selection of rugged power solutions for ground based defence vehicles.
Testing More Electric Aircrafts (MEA)
As flight systems evolve from traditional hydraulic to being electrically controlled/ powered, they must meet the same stringent standards as existing models. MEA applications demand high power density, reliability and availability whilst aiming to reduce weight, complexity and fuel consumption. For these reasons, it is crucial that accurate test equipment is used during design and development.
The 4 quadrant EAC-ACS-4Q is able to provide frequencies up to 1kHz, with superimposed harmonics up to 5kHz. The wide frequency range is ideal for replicating an aircraft's variable frequency generator. Each of the unit's three phases is individually programmable for voltage, frequency, current and phase angles. This allows virtually any conceivable power condition to be recreated.
When researching battery powered DC equipment, using real batteries can be unreliable and time consuming. To compare experiments like for like, control variables such as state of charge and temperature need to be conditioned and accurately measured before testing. With a battery emulator this isn't a problem, as they replicate the real world behaviour of batteries.
Bidirectional systems such as the G5-RSS will accurately simulate an MEA's battery pack up to 3kV. Various chemistries can be replicated as well as different power, voltage and current levels. Automated test procedures and hard to reproduce operational states can be run at the push of a button. The performance of devices such as DC-DC converters, inverters, motors and DC subsystems can be isolated and analysed.
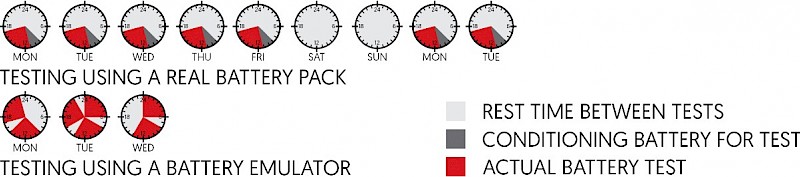
Rugged Vehicle Mounted Power Units
Military land vehicles require ultra-reliable power supplies for mission critical electrical equipment. On request, rugged solutions can be provided with mechanical modifications to protect the power supply against shock, vibration and humidity.
Many previous modifications have been carried out on existing products. A special version of the LAB-TC has been developed to power on-board transmitters in defence vehicles. The system has been used many times since, operating from AC generators to provide a DC output. Each unit is able to withstand up to 30g of mechanical shock across X, Y and Z axes. The PSU operates from temperatures as low as -10°C all the way up to 55°C.
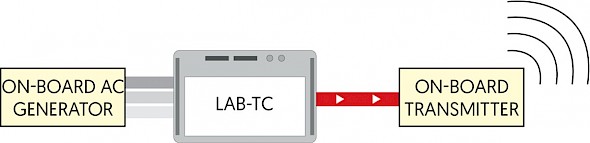
A special DC-AC inverter was developed to provide back-up power for ancillary electrical equipment on military vehicles. The inverter provides a true sinewave output of 230VAC at 50Hz from a 24VDC battery input. The system provided 1kVA continuously, though usefully the inverter has a high peak capability for an extended time period (1.45kVA for 30mins and 1.6kVA for up to 10mins).
Voltage Drops and Interrupts Testing
Sudden voltage interruptions can cause unexpected behaviour in safety related electronics, such as brake and door control systems. Supply line disturbances may have causes. This includes the sudden opening of contactor lines switches, or an additional switch on of a large capacitive load.
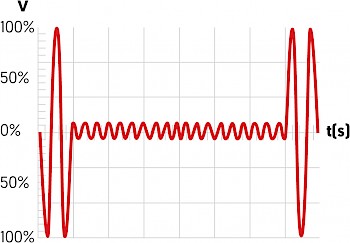
Programmable power supplies from ETPS can recreate almost any operating condition, so that any issues are identified and fixed during the R&D process. Scenarios such as brownouts can be created using EAC-S or EAC-3S AC sources. The linear units have common waveforms pre-installed, with the ability to edit V and I parameters. Output frequencies up to 2kHz are possible.
Real world DC voltage drops within fractions of a second can be simulated using the G5-SOURCE. The fast dynamics of the unit, combined with an embedded function generator, allow virtually any DC waveform to be created. This is particularly useful when testing electronic landing gear.
Complex DC waveforms can be implemented via the G5-SOURCE's embedded function generator. Voltage/current and voltage/power relationships can be programmed against time. Parametric programming is also possible, where instead of the time axis an input variable (VIN, IIN or PIN) can be selected.
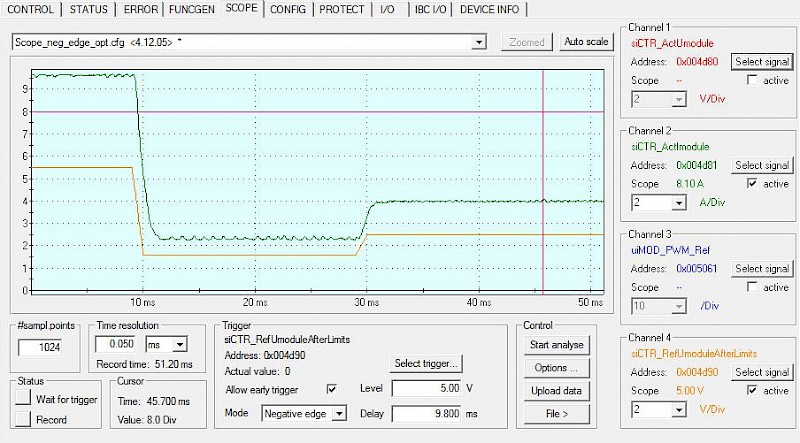
Lifetime Testing of Components
A lifetime test is where an electrical system or component is operated for an extended period of time, to detect common problems late in life. Mean Time Between Failures (MTBF) can be calculated, so that aircraft electronics are replaced before the point which they are likely to fail.
Real world usage conditions can be programmed into both AC and DC power supplies. An integrated SD card slot is available for PSUs such as the EAC-S and LAB-HP. This allows simple text script files to be written which implement voltage, current and time characteristics on an automated loop. One application this is often used for is ON/OFF testing of landing lights.
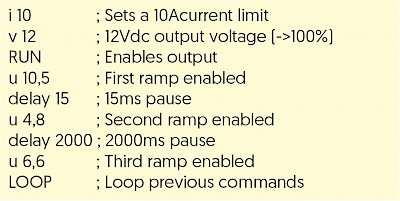
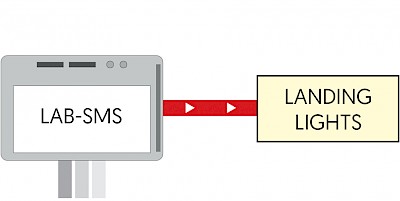
Most AC loads and DC loads from ETPS have programmable front panel memory as standard. Users can save and recreate common test set-ups. All of our AC models have an adjustable power factor, which allows a leading or lagging power factor to be set with adjustments from unity to 0 for selected models. A crest factor mode is also provided to test peak currents.